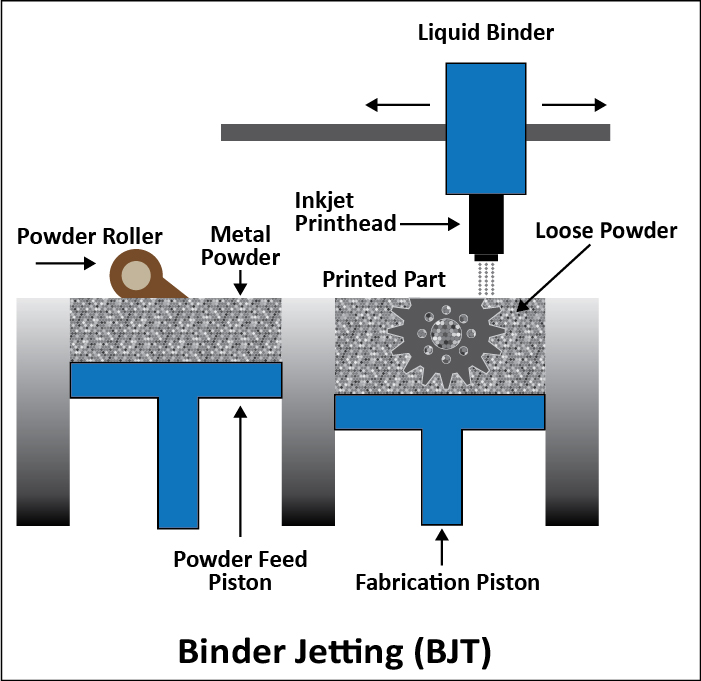
Binder jetting technology (BJT) utilizes a printhead to selectively deposit a liquid binding agent onto a thin layer of powder particles, forming a loosely bound “green part” to be sintered later in a furnace. BJT may utilize metals, ceramics, or composites to build components. The process begins with a 3D CAD model which is numerically sliced into discrete layers. The printhead selectively deposits a binder to the powder, layer by layer, until the components are complete. After printing, metal BJT parts require debinding and sintering to consolidate the material into a near full density geometry. BJT is used when increased throughput or increased print area is required. BJT generally utilizes standard MIM powders.
Advantages of Binder jetting technology
Binder jetting is particularly well-suited for the production of complex parts with intricate geometries and internal features. Binder jetting is a cost effective manufacturing technology that permits production of components from a large variety of common and affordable materials, including stainless steel, tool steel, copper, nickel titanium and aluminum alloys, and ceramics. Binder jetting enables batch production, meaning manufacturers can produce hundreds, even thousands of PM components per day or multiple versions of a single parts in a single print. Binder jetting can generally produce higher volumes of components faster than other metal additive manufacturing technologies, while being cost affective as all unused powder in binder jetting can be repurposed for future printing jobs, resulting in less waste and lower material costs.
Disadvantages of Binder jetting technology
Metal binder jetting parts may have lower mechanical properties due to their higher porosity as compared to fusion based metal additive manufacturing processes. Binder jetting parts may not have surfaces that are as smooth as compared to other metal additive manufacturing processes as-sintered, sometimes requiring secondary finishing processes to improve surface conditions.